HISTORY
Our vision guidance products of today are the result of a long series of developments that started in 1993 with a science-based research project to investigate the feasibility of using the then new technology of computer vision in the relatively unstructured agricultural field environment. We called that project “Plant scale husbandry” as it was based on the hypothesis that navigation along crop rows and individual plant treatment could be done using computer vision without the need for a global sensor such as GPS. Whilst not essential for the projects aims, we also gave our experimental vehicle the ability to run fully autonomously within the field. This project laid the foundations for subsequent work. We publicly demonstrated spot spraying of individual cauliflower plants from our autonomous vehicle in 1996.
Subsequent work had a more application orientated emphasis. We chose inter-row implement guidance as the technical challenges of maintaining lateral alignment of an implements from a manually driven tractor were less than other applications. Specifically, we chose weed control by inter-row cultivation as there were no legislative barriers to commercial take up and there was a small but growing market from organic farmers.
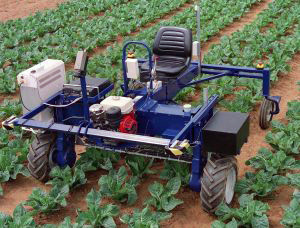
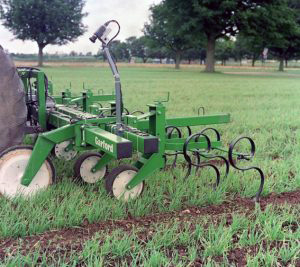
Our initial work on inter-row guidance for mechanical weed control was taken up by Garford Farm Machinery and Robydome electronics in 2001 when the first Garford Robocrop hoe was sold. Research continued in parallel with commercial exploitation so that the scope and capability of the technology grew rapidly. By 2004 the first commercial systems following multiple planter bouts were being sold and the range of crops went from sugar beet and cereals right through to onions and carrots.
Our idea to synchronize a rotating blade with regularly spaced individual crop plants using machine vision led to another collaborative research project which started in 2005. This went well and the first commercial in-row weeding machines were sold in 2008. The first machines were hydraulically driven, but we have subsequently gone on to introduce an electrically driven version which offers higher speeds and greater precision, albeit with reduced maximum torque.
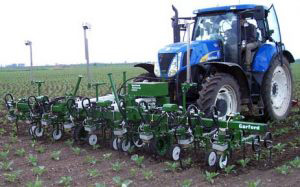
In response to requests grower organisations who were concerned about the loss of herbicides, we returned to spot spraying in 2008 with another collaborative project. The principle application was the control of broadleaf weeds, particularly volunteer potatoes in the slow emerging drilled crops such as carrots and onions. This time we based our spot spraying platform on a wider (6m) implement mounted on a conventional tractor as we felt the economics for autonomous operation did not stack up at that time.
Technical progress was good and we successfully treated several tens of hectares of commercial crops.
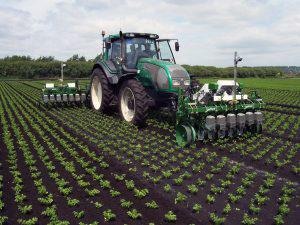
So far agronomists have generally managed to keep weeds under control in these crops by careful use of herbicides that have retained approval. Conventional uniform application of selective herbicides from boom sprayers is always faster than spot spraying conducted from a relatively expensive spot sprayer. Commercial take up, in contrast to our mechanical weeding applications, has been poor. However, as restrictions continue to be placed on herbicides the benefit of applying those that remain in a highly targeted manner will grow.
Spot spraying remains an active research area for us and we expect to see continuing improvements in performance.
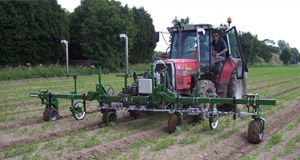